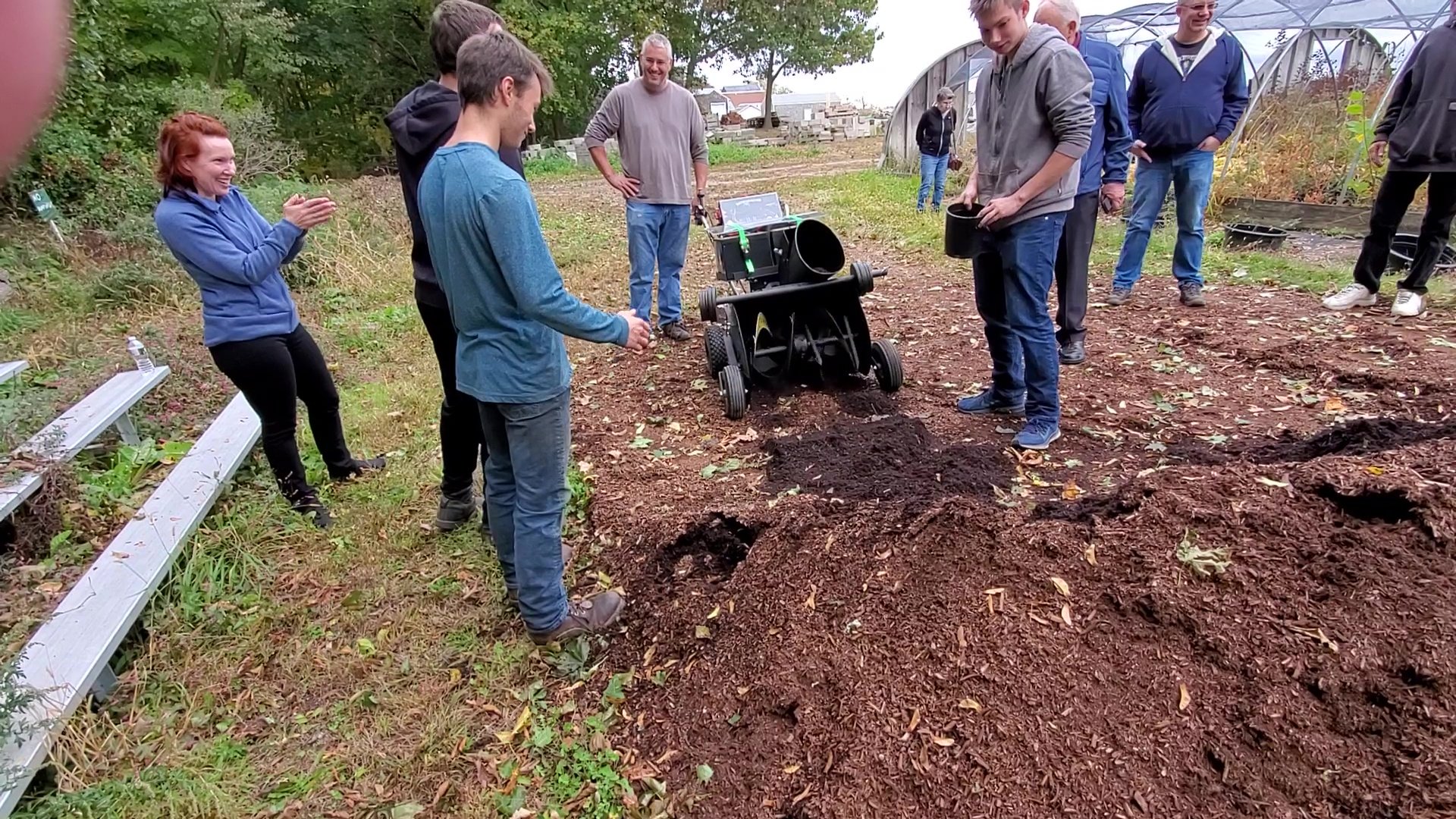
Snow mulcher
This project was funded through a SEMAP T.I.E. grant, in collaboration Bristol Aggie High School. Barry Griffin and a group of students converted a 6.5hp gas-powered snowblower power head and drive train to an all-electric 8hp mulch spreader. This required extensive planning, problem-solving, electrical engineering, and metal fabrication.
Abstract
Fossil fuel motors have known environmental impacts when compared with electric motors powered by batteries, and solar power.
Gas engines are noisy, which limits the starting and stopping time for work being done in certain suburban and urban communities. Electric driven machines are very quiet and produce no fumes or spills.
Gas engine and internal combustion machines require a gearbox transmission or other mechanism to reverse direction of the work. Electric motors can be reversed simply and relatively inexpensively.
We believe small farms will require new specialized tools, design engineering, and technicians in order to remain competitive. We hope to learn the techniques and methods that allow us to invent and design such tools in the future and for our local farms.
The method
A donated Ariens snowblower was cleaned and repaired as needed. A group of 6 students worked with Bristol Aggie shop instructors and outside mentors and consultants to design and build a conversion bracket. The bracket duplicated the footprint of a standard 6.5 hp IC gas engine but with a mounting flange for an 8 hp 48 VDC electric motor. The motor and bracket were designed to allow the attachment on a battery box for four (4) 12 VDC tractor batteries and control wiring, ON/OFF switch, Ammeter, Emergency OFF switch, direction and speed control. The motor and controls was tested and then mounted to the head unit of the snowblower, without the blower. The drive system was tested to verify that the PTO function worked.
The snowblower or other Ariens implement was mounted and tested. We tested the snowblower in reverse to see if reversing the chute and fan would allow the snowblower to move forward and at the same time feed material down the chute. The traction force of the machine is calibrated with a spring scale and ammeter so that the ammeter can then be used in determining the force required to operate existing and new tools we may design in the future.
This conversion provided:
A prototype demonstrating a method to convert typical fossil fuel driven farm machinery to electric power.
An experiment to learn the agricultural benefit by reversing the snowblower fan and feeding the discharge chute with compost or other materials for use in bed preparation or other mixing applications.
A powered wheeled electric PTO for use in:
Greenhouse
Developing and testing other special tools in the future.
Developing a program and curriculum in farm tool and machine design.